High-rise glazing has seen big advancements in strength and design over the years, showcasing the best of modern engineering. However, even with high-quality materials and expert installation, there are still challenges to overcome.
A puzzling issue in the glazing industry is the random glass breakage caused by nickel sulphide inclusions (NiS). These failures often leave property managers and building owners scratching their heads. At Apex Facades, we’ve encountered this kind of breakage many times, and we’re here to shed some light on what’s going on – and how we can help.
What are nickel sulphide inclusions?
Nickel sulphide inclusions are microscopic impurities that can form during the manufacturing process of tempered glass. Even when glass manufacturers adhere to stringent quality controls, small amounts of nickel can sometimes find their way into the raw materials. Under high temperatures during the glassmaking process, these nickel particles react with sulphur to form nickel sulphide.
Often, these inclusions aren’t a problem. But, over time, temperature changes, structural stress, and the natural aging of the glass can cause the nickel sulphide to expand. This expansion creates internal tension within the glass, which can eventually lead to a sudden and often dramatic breakage – especially in high-rise buildings.
Why do nickel sulphide breakages seem so random?
One of the most frustrating aspects of these kinds of breakages in high-rise glazing is the unpredictability. Glass can shatter months or even years after installation, seemingly out of nowhere. Here’s why:
- Invisible to the naked eye: Nickel sulphide inclusions are microscopic and can’t be detected during standard inspections. This makes it nearly impossible to identify affected panels before failure.
- Environmental triggers: Factors like rapid temperature changes (thermal shock), exposure to direct sunlight, or even building vibrations can exacerbate internal stresses, triggering breakages.
- Time-dependent nature: NiS inclusions don’t cause immediate breakages. Instead, the expansion process happens slowly over time, meaning the glass can fail long after installation.
- No predictable pattern: There’s no uniformity as to when or where breakages occur, adding to the randomness. One panel may fail in a decade, while others remain fine forever.
The science behind nickel sulphide and glass
Nickel sulphide inclusions can be introduced into glass during the manufacturing process in two main ways:
- Raw material contamination: Nickel sulphate can enter the glass-making process as an impurity in raw materials like sand, soda ash, and limestone.
- Additive for colouring: Nickel compounds, including nickel sulphate, can be intentionally added to glass to achieve specific colours. These compounds impart a blue or violet hue, which is often desirable in decorative applications.
While nickel sulphate itself does not significantly alter the structural properties of glass, its interaction with other elements during the melting process can affect the viscosity and homogeneity of the final product. These variations can, over time, contribute to spontaneous glass breakage.
Identifying nickel sulphide inclusions
When glass containing nickel sulphide inclusions breaks, it can exhibit a characteristic “butterfly” fracture pattern, which can help identify the cause of failure. Here’s how detection works:
Pre-breakage detection:
- Infrared thermography: Detects inclusions based on thermal conductivity differences.
- Ultrasonic testing: Uses high-frequency sound waves to identify flaws.
- X-ray imaging: Spots denser materials like nickel sulphide within the glass.
Post-breakage analysis:
- Visual Inspection: Inclusions are often visible at the fracture origin.
- Microscopic Examination: Provides confirmation of an inclusion at the break site.
The distinctive “butterfly” pattern forms due to the internal stresses exerted by nickel sulphide’s phase transformation. This symmetrical cracking originates from the inclusion point and extends outward, making it an important forensic clue in glass breakage investigations.
The role of heat soaking
To mitigate the risk of nickel sulphide breakages, some manufacturers subject tempered glass to a process called heat soaking. This involves heating the glass to around 280°C and holding it there for several hours. The idea is to accelerate the expansion of any NiS inclusions, causing the affected glass to break in a controlled environment rather than after installation.
Heat soaking is effective, but it’s not foolproof. It can reduce the risk of spontaneous breakages but doesn’t guarantee a 100% elimination of the issue. At Apex Facades, we always recommend using heat-soaked glass for high-risk applications, such as high-rise glass installations or areas with significant environmental stressors.
How Apex Facades handles nickel sulphide breakages
It can be stressful and disruptive when high-rise glass fails unexpectedly. As specialists in high-rise glass replacement, Apex Facades is equipped to address NiS breakages efficiently and safely, minimising the impact on tenants, clients, and the public.
- Rapid response team: Our experienced rope access technicians can quickly assess and replace broken panels, even in the most challenging high-rise environments.
- Minimal disruption: Using innovative rope access techniques, we can perform most repairs without road closures, large cranes, or significant interruption to the building’s operations.
- Specialist equipment: From vacuum lifting systems to pulleys and hoists, we have the tools to handle even the largest glass panels.
- Australian standards compliance: We work exclusively with high-quality, Australian-standard materials to ensure durability and safety.
- Preventative consultation: If your building has experienced NiS breakages, we can advise on heat-soaked replacements or other strategies to reduce future risks.
Why Choose Apex Facades?
At Apex Facades, we combine technical expertise with innovative solutions for high-rise glazing. Our rope access specialists are trained to handle even the most complex glass replacement challenges, ensuring safety, efficiency, and quality in every project.
If you suspect your building is at risk of spontaneous glass breakage or need expert advice on high-rise glazing solutions, contact Apex Facades today.
Got a project in mind?
Get in touch with the vertical professionals for all your speacialised construction needs.
Get a quote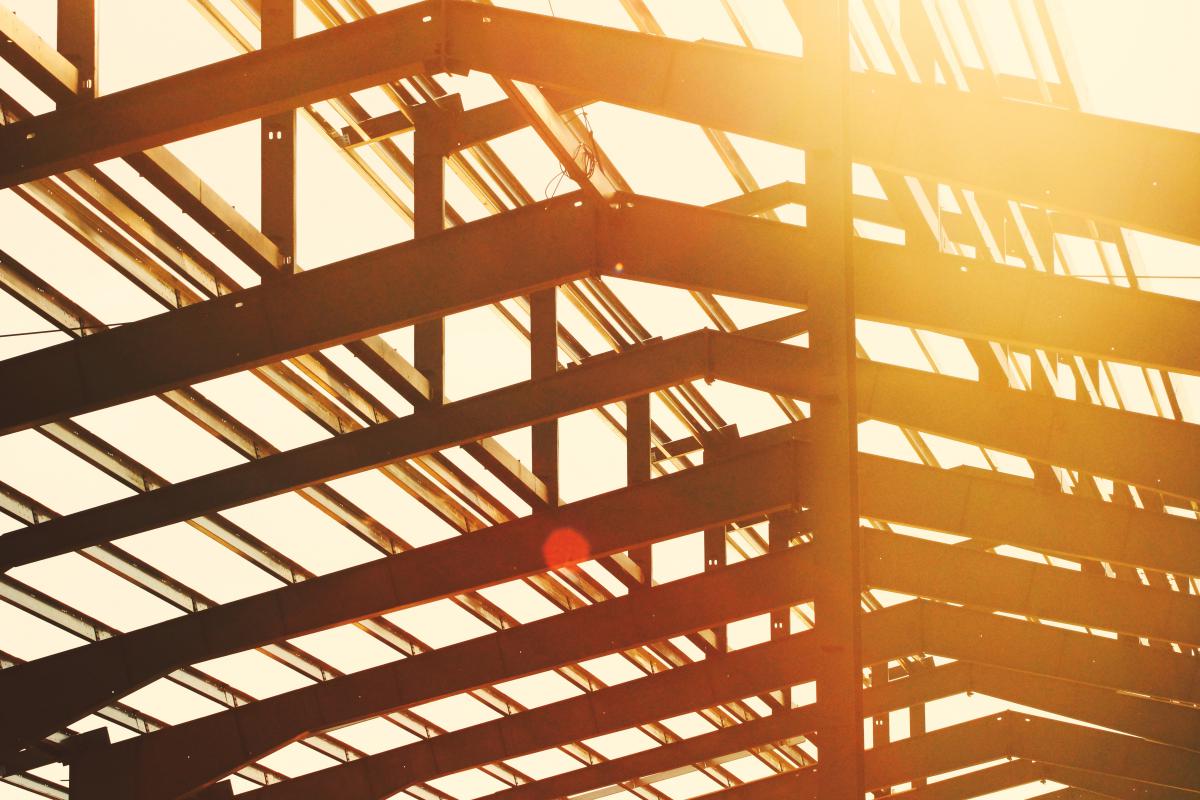